Palette Architecture Pushes the Limits of Single-Family Modular Construction with Shift | House

Architects & Firms
Building a new family home is never easy. Material deliveries often get delayed. Contractors can prove less than reliable. Maintaining quality control can be difficult throughout the tumult of an active construction site. The pandemic, with its disruption of global supply chains and social distancing measures, compounded these, and other, issues. Shift | House, located in East Hampton, New York, and designed by New York City and Los Angeles–based firm Palette Architecture, charted a different course by deploying modular construction.
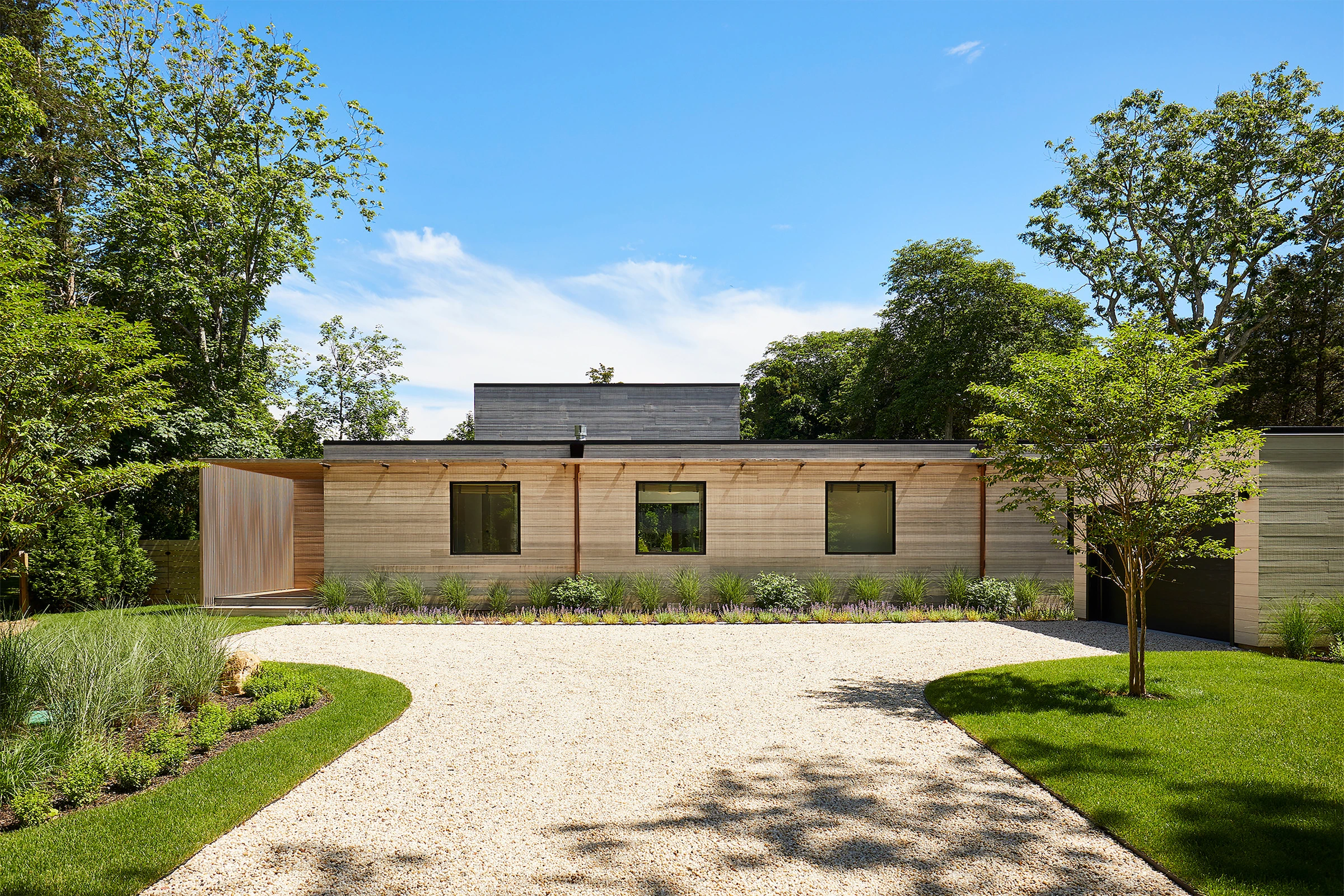
Shift | House is accessed via a gravel driveway, with a stand-alone garage. Photo © Jody Kivort
Construction on the 1,600-square-foot dwelling began in December 2022 and concluded in June 2024. The client, a family that Palette had worked with before on a townhouse renovation in Brooklyn, wanted a second home to spend extended periods of time away from the city. They were drawn to Springs, a relatively understated corner of East Hampton where they found an undeveloped half-acre lot. According to the architect, the client prioritized an efficient use of space across a modest building footprint and the ability to maintain a sense of awareness of activities across the house. “The family expressed this idea that they’re most comfortable in a space where they could stay connected, be it through visual, sensory, or sound cues, while engaging in their own separate and private activities,” notes Palette founding partner Peter Miller.
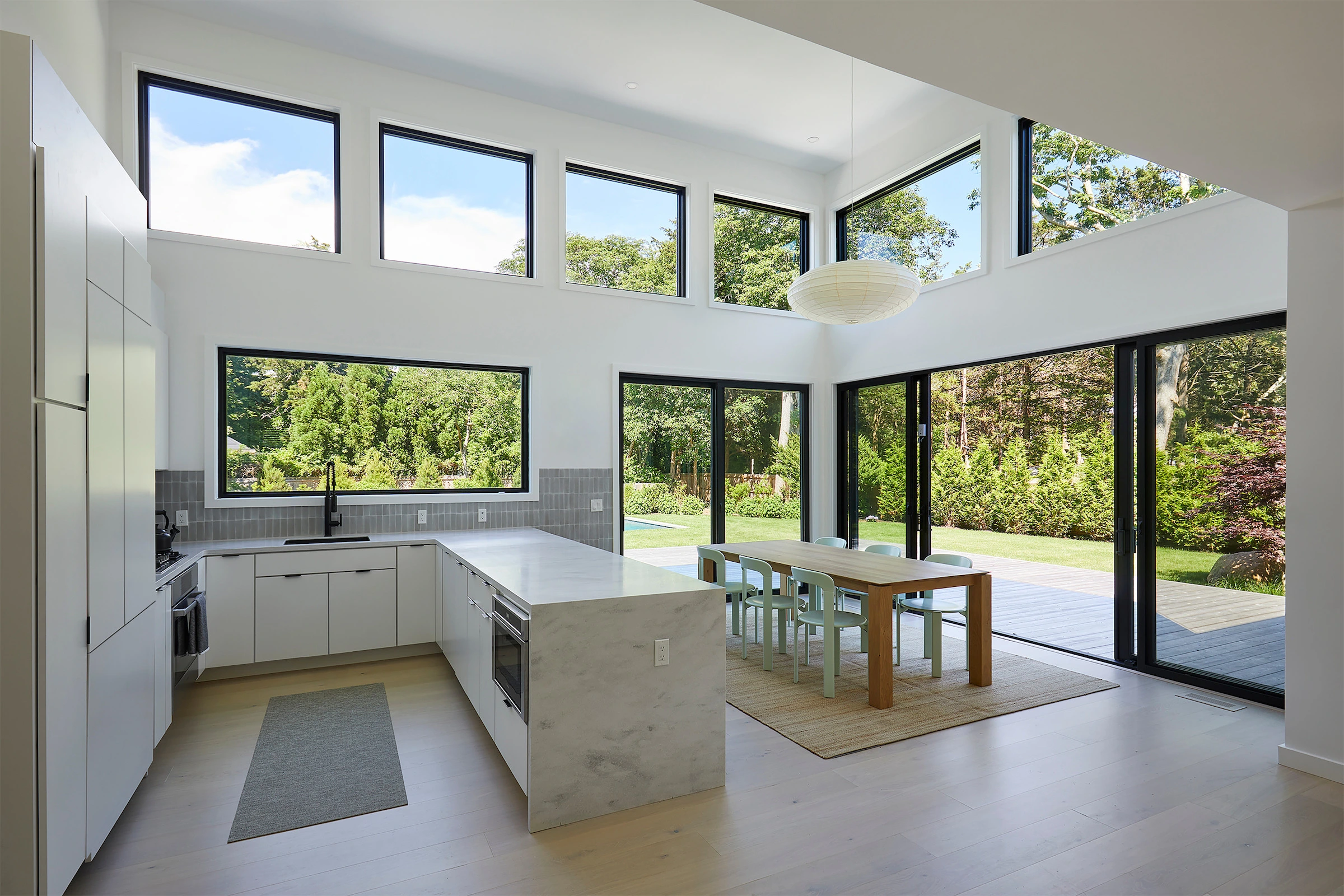
1

2
The living and dining room was transformed into a double-height space with the help of structural insulated panels (1). The primary bedroom opens to the backyard with sliding glass doors (2). Photos © Jody Kivort

Tile work, including that in the bathrooms, was completed on site. Photo © Jody Kivort
Palette has designed several single-family residences with modular construction methods in New York. One of the firm’s greatest challenges is transcending the restrictive dimensions of volumetric units—here they are 64 feet long, 15-and-a-half feet wide, and approximately 9 feet tall —to create a variety of spaces within. They achieve this effect at Shift | House with an L-shaped plan, where the modules that house bedrooms and bathrooms hinge from a living and dining room made into a double-height space with the help of prefabricated structural insulated panels. The straightforward plan offers clear sightlines and ample daylight, made all the brighter by sliding doors at the rear elevation, which open onto an expansive backyard porch.
Although modular and prefabricated construction can set strict parameters in terms of building form, these methods can significantly expedite construction schedules and reduce overall project budgets. The volumetric units here were integrated with a fully assembled kitchen, electrical work, plumbing, and oak millwork within a controlled factory setting—in this case, located just outside of Scranton, Pennsylvania. Once complete, the modules were trucked to the site, and, over the course of just three hours, craned into position atop the foundation and structurally fastened together. Over the following days, the utility connections were finalized and the building envelope, which arrived with exterior waterproofing, sheathing, and insulation, was clad in thermally treated Accoya wood fabricated to resemble the weathered cedar shingles and boards common in East Hampton. Certain interior finishes, like tile work and the fireplace, were completed on site.
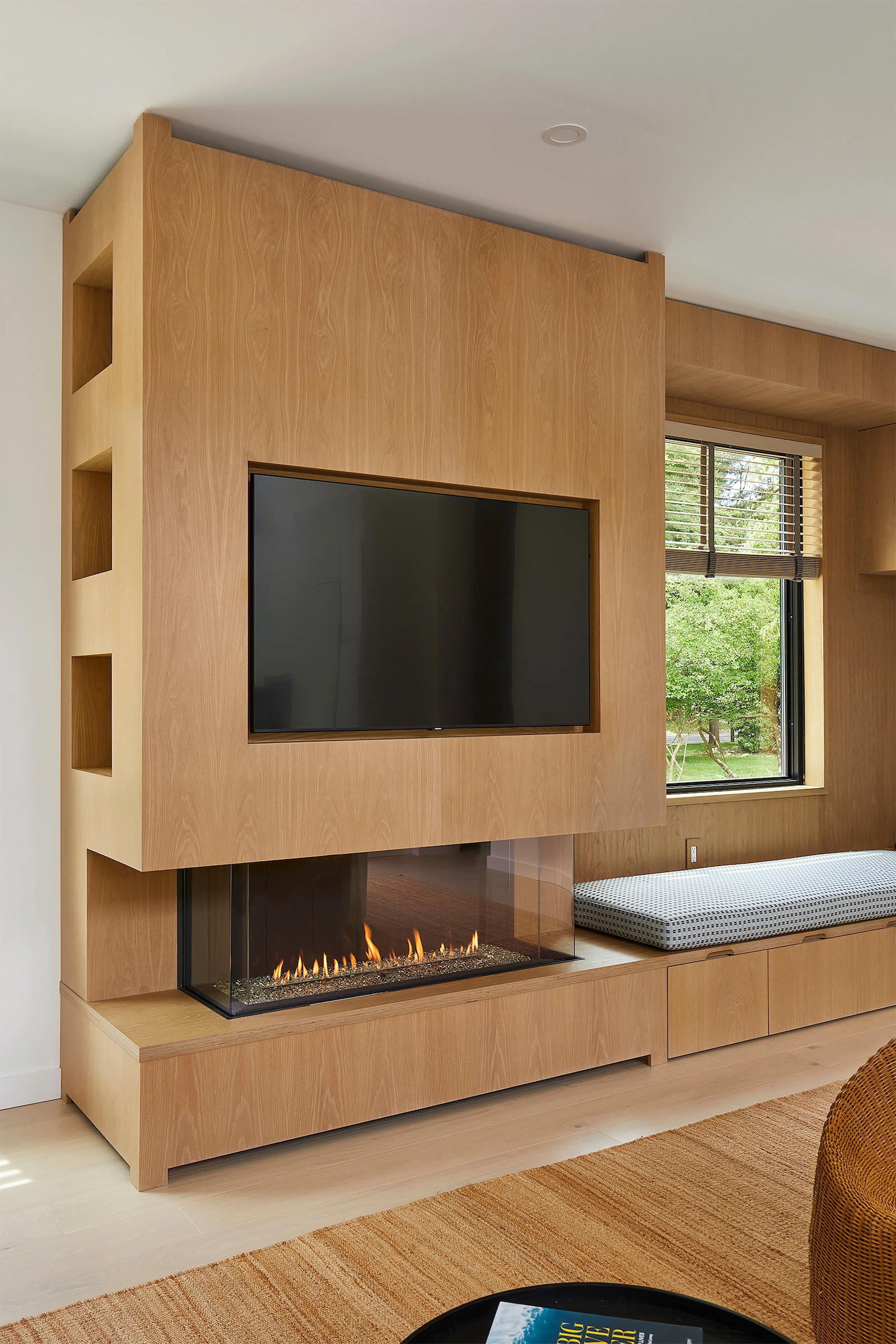
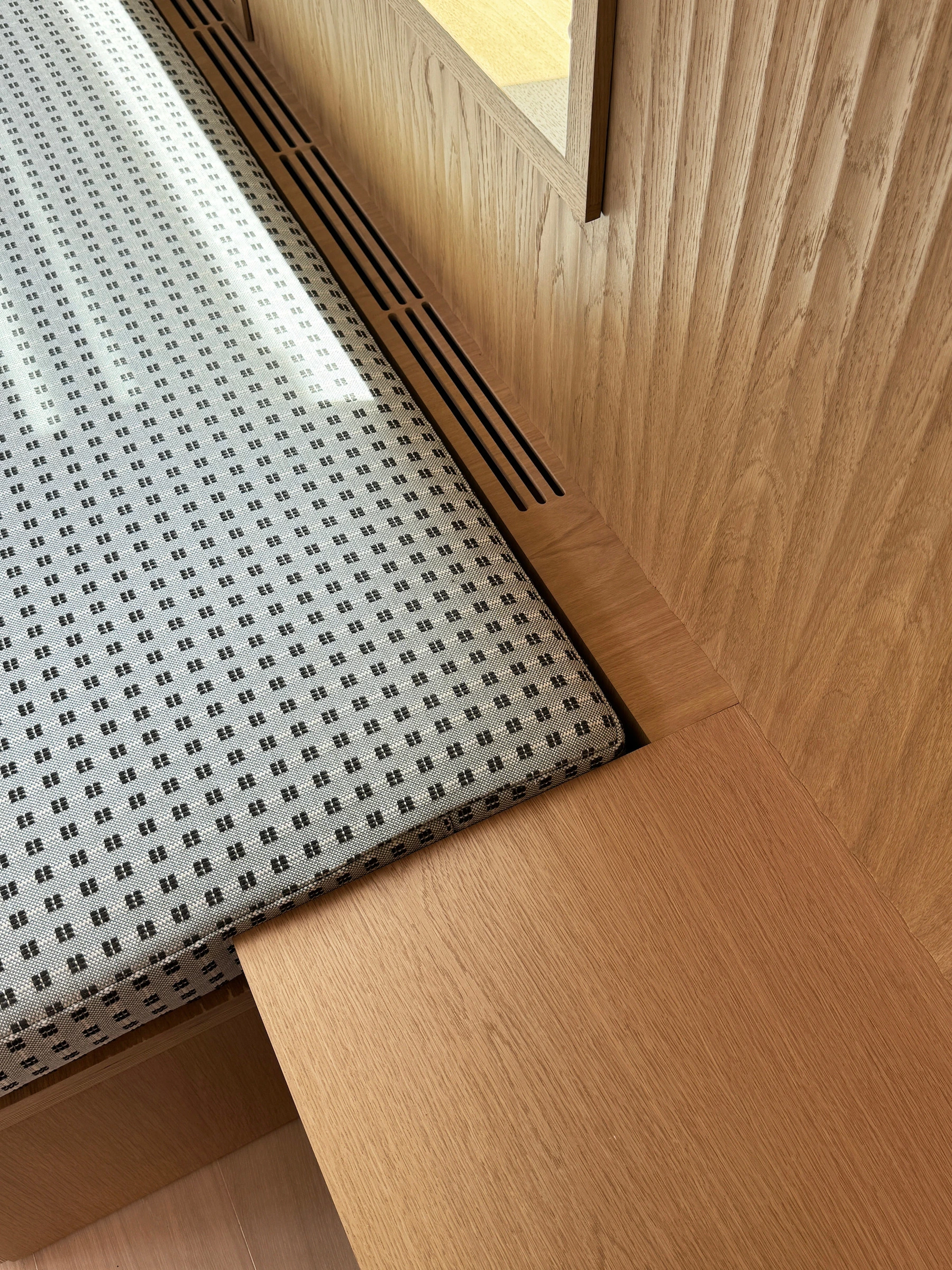
2
Millwork across the project was fashioned within a factory setting. Photo © Jody Kivort
Fitting all these pieces together required tight tolerances, and, with it, a greater workload prior to construction. But, Miller says, the extra labor on the front end paid off—to the tune of approximately 15 percent in cost savings and a 20 percent reduction in the total construction schedule.
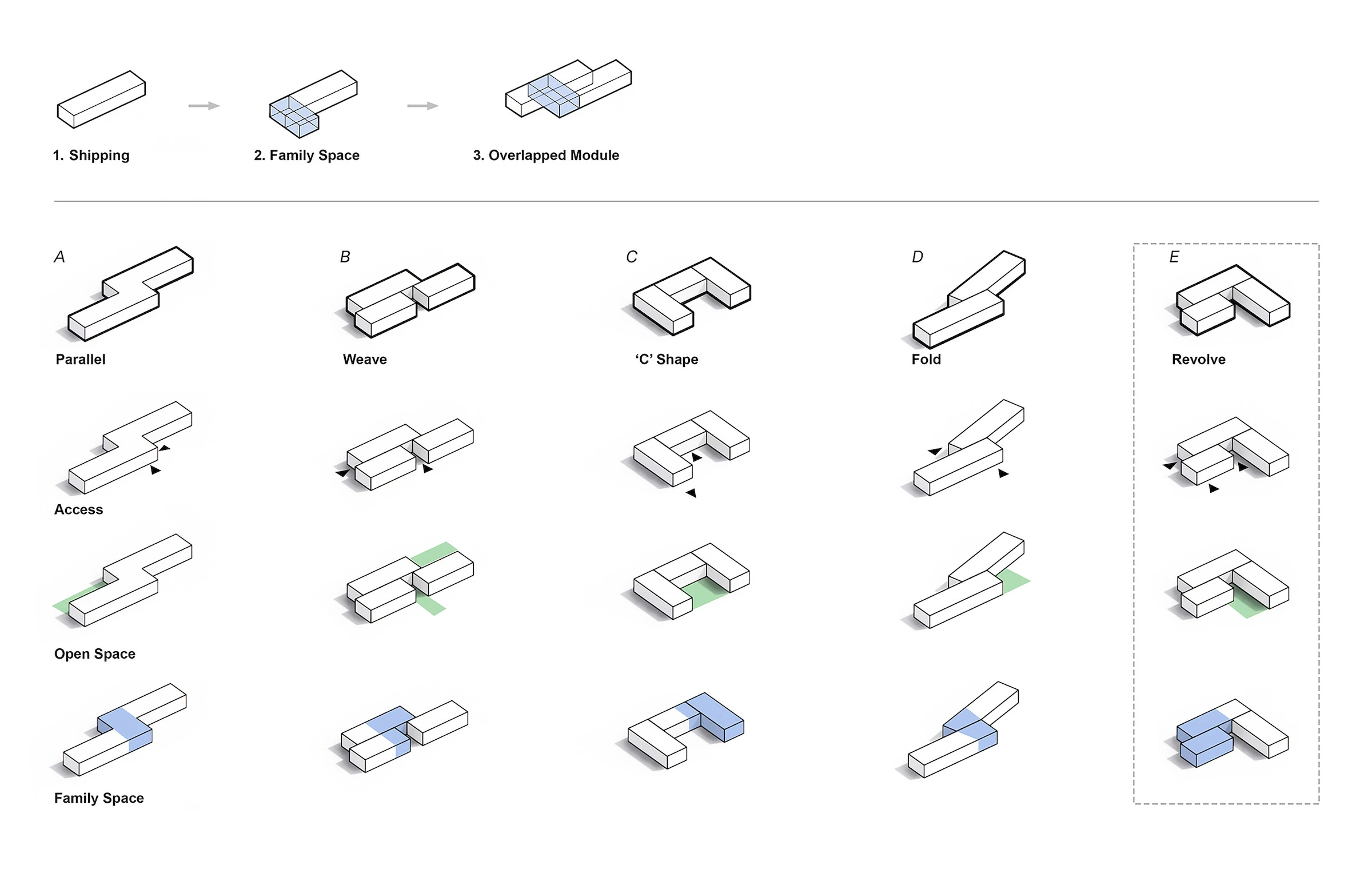
The design team researched various iterations of modular configurations. Image courtesy Palette Architecture
While there are many benefits of modular construction, there are still several hurdles hindering larger adoption—such as cultural perception. “There is a concern with clients that a modular project will resemble a mobile home," Miller notes. "You have to bring them along and show that the final result can really look like any other house, especially when you use structural insulated panels to break out of restraining dimensions."
Considering the refined result achieved with Shift | House, others would be wise to take notice.