Timberlab’s New South Carolina Mass–Timber Fabrication Facility Reaches Full Capacity

Timberlab’s new 75,000-square-foot plant in Greenville has doubled the national fabrication capacity of large glulam components. Photo courtesy Timberlab
Mass timber is still a small segment of the construction industry in the United States. A recent congressional report counts 1,753 mass-timber buildings in the country as of March of last year. “For context,” the report says, “5.9 million commercial buildings were constructed in 2019 alone.” But the market is growing. According to one estimate, mass-timber construction in the U.S. has doubled every two years for the past five years. Timberlab, a provider of mass-timber engineering, fabrication, and installation services, is betting that this trajectory will continue.
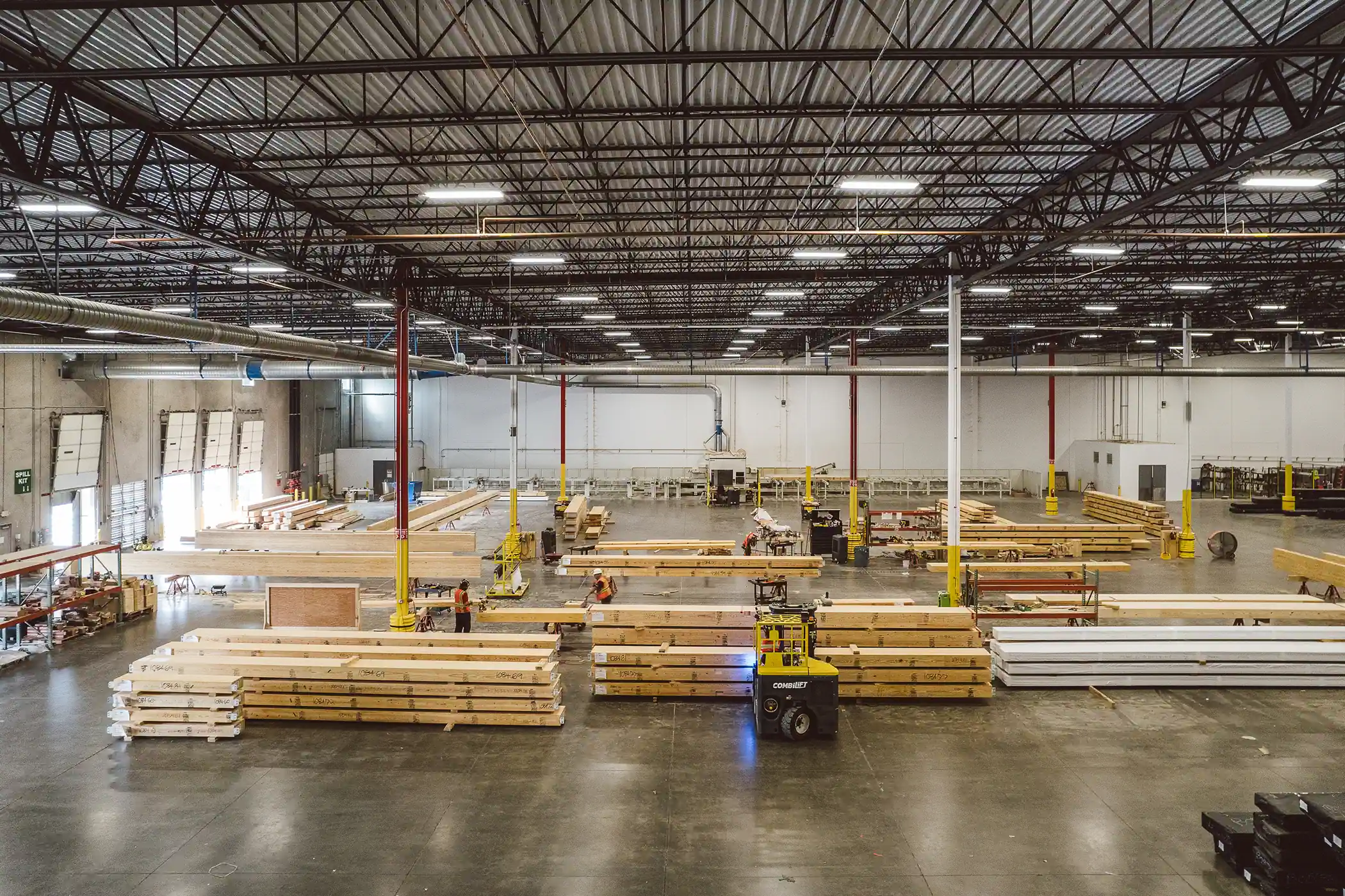
At the Greenville plant, Timberlab uses CNC machines to mill non-fabricated glulam billets, transforming them into custom, project-specific components that are then assembled on the building site. Photo courtesy Timberlab
Earlier this month, the company announced that a glulam fabrication plant it opened just over a year ago in Greenville, South Carolina, was now operating at full capacity, with the ability to support one million square feet of mass-timber construction annually, making it the largest such facility east of the Mississippi, and only one of three similar plants in the Southeast. Timberlab says that the facility has doubled the fabrication capacity of large glulam components for mass-timber structures nationally.
First started as a timber-focused division of San Francisco-headquartered general contractor Swinerton in 2016, and then known as Swinerton Mass Timber, Timberlab opened its first fabrication plant in Portland, Oregon, in 2020, followed by its formal launch as a wholly owned subsidiary in 2021. In addition to the Portland and Greenville plants, Timberlab recently acquired two glulam manufacturing facilities from American Laminators in Oregon. It has also announced plans to open a cross-laminated timber (CLT) manufacturing operation in that state’s mid-Willamette region. LEVER Architecture, a Portland-based firm known for its work in mass timber, is designing the new CLT facility, which is expected to open by 2027.

Photo courtesy Timberlab
Timberlab chose Greenville due to the region’s abundance of southern yellow pine, its existing network of glulam manufacturers, and its proximity to high-growth East Coast construction markets. At the South Carolina plant, Timberlab uses CNC machines to mill non-fabricated glulam billets, transforming them into custom, project-specific components that are then assembled on the building site. Timberlab can source the glulam from nearby producers or from its recently acquired plants in Oregon. “It is easy to send non-fabricated glulam across country by rail,” explains Chris Evans, Timberlab president. “But Greenville is not exclusive to glulam manufactured at our facilities,” he adds. “We will do the best procurement for our clients.”
Among the first projects supported by the Greenville plant is a 67,000-square-foot office building for the LS3P-designed Live Oak Bank in Wilmington, North Carolina, and a 42,000-square-foot career and student center at the University of Southern Maine designed by Elkus Manfredi. Projects with mass-timber components milled at Timberlab’s Pacific Northwest fabrication plant include Atelier Jones’ Heartwood, an eight-story, 216-unit apartment building in Seattle that features unusual all-wood mortise-and-tenon joints.
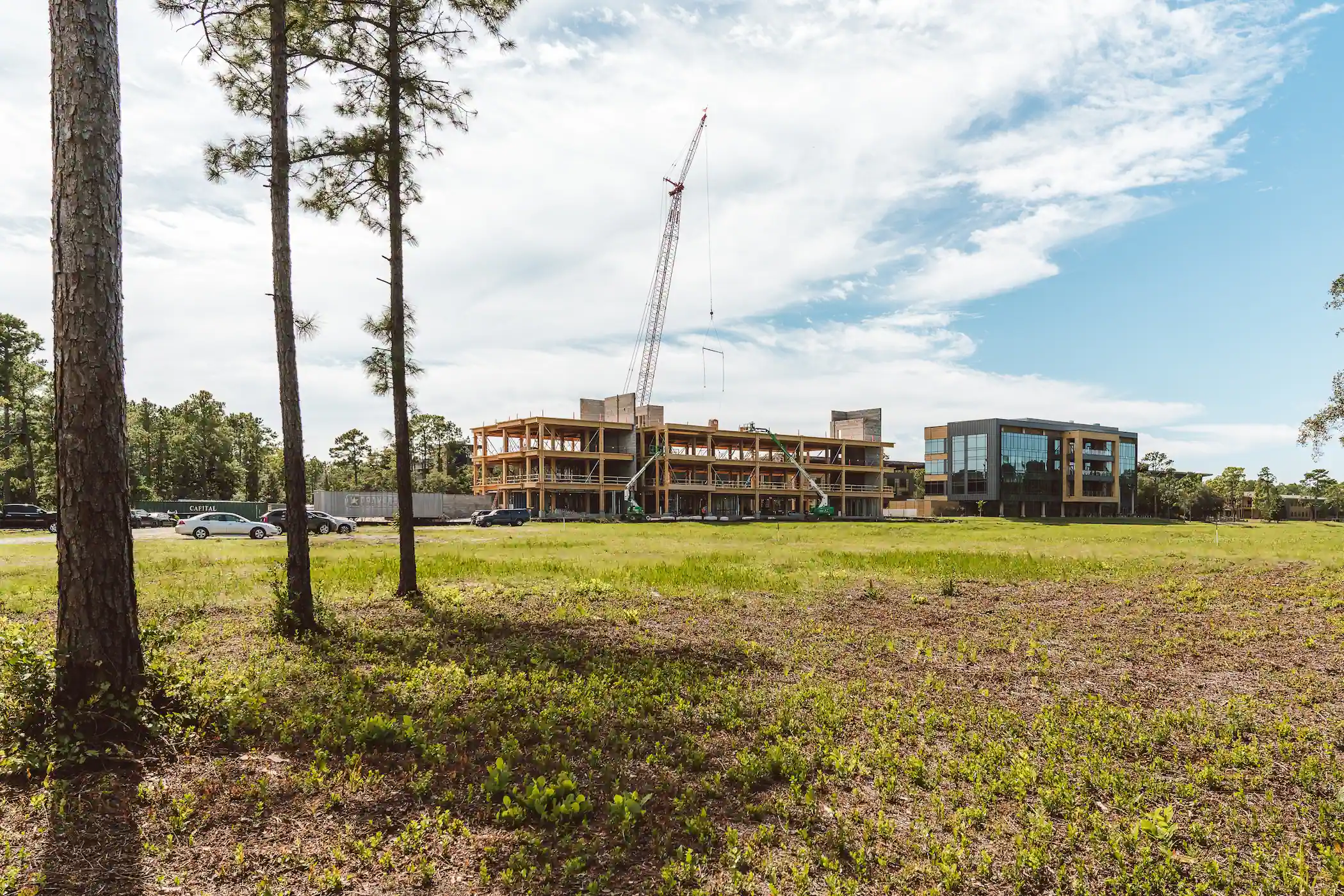
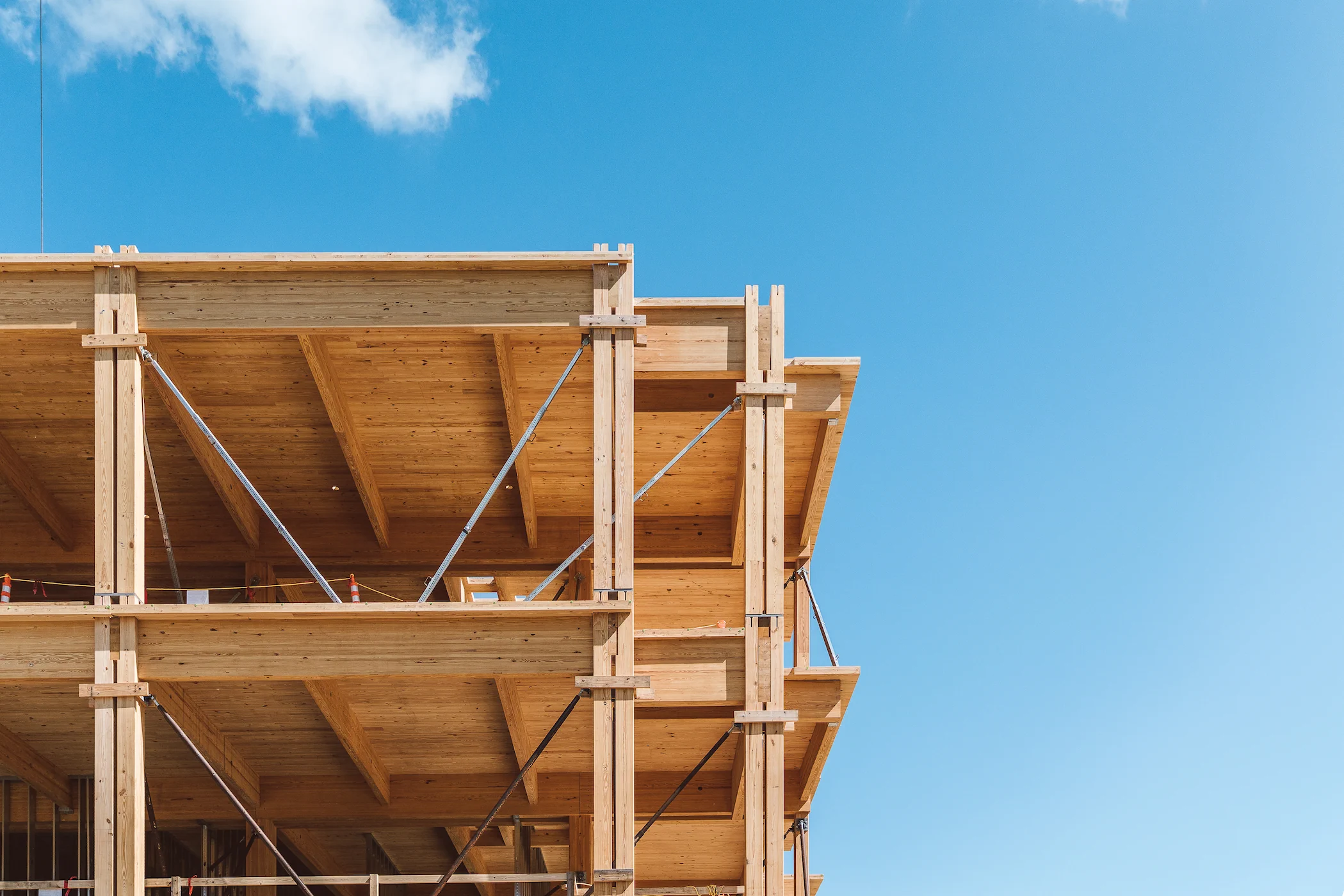
An LS3P-designed office building for Live Oak Bank in Wilmington, North Carolina, is among the first projects supported by Timberlab’s new Greenville plant. Photo © FLOR Projects
If Timberlab’s expansion sounds rapid, Evans maintains that the company’s evolution has been measured and methodical, spanning eight years. Its investment in the supply chain, funded by shareholders (both Timberlab and Swinerton are employee-owned), will ultimately make mass-timber buildings more affordable, he says, while helping spur greater demand. “It is a chicken-and-egg situation,” he says. “You need to have the investment to support the market’s growth.”