Continuing Education: Bio-Based Materials

Bio-based building materials used to be mainstream. The roof of the Pentagon (which was built in the early 1940s) is insulated with horsehair. Until the mid-20th century, the great majority of construction components were biomass, primarily wood and agricultural fibers such as straw and hemp—health- and environment-wise, all good stuff. (That’s assuming responsible land stewardship.) Then along came oil, laying out a smorgasbord of new and newly available materials—and a banquet of consequences: dozens of chemicals that pose health risks, ranging from skin, eye, and throat irritation to infertility, asthma, and cancer are now widespread in building materials. From an environmental perspective, just three of construction’s most common components—concrete, steel, and aluminum—account for 23 percent of global carbon emissions. As the AEC sector faces up to a toxin-laced built environment on the wrong side of the carbon ledger, bio-based materials are looking better than ever.
There are some nifty new options entering, or about to enter, the market. A self-supporting bio-composite facade panel for commercial buildings, developed by Arup and GXN Innovation, is designed for disassembly and recycling/reuse at the end of its life cycle. Carbon-sequestering structural blocks—under development by Prometheus Materials (a spin-off of a research program at the University of Colorado) and SOM—use an algae-based concrete alternative. A high-performance glazing system being designed by University of North Carolina architecture professor Kyoung Hee Kim, integrates carbon-storing microalgae screens into biochromic windows. Patent-pending products developed by Mycocycle, a materials startup, leverage the natural functions of mycelium (the root structure of fungi) to transform a range of construction wastes—including gypsum, asphalt, and plastic polymers—into toxin-free new materials.
But, exciting though these prospects may be, some of the most significant opportunities for bio-based building are already on the ground, literally. Agricultural wastes such as straw (the stems of grain crops, not to be confused with hay, which is dried grass used for animal feed) and hemp hurd (the woody, inner part of the stem, a by-product of processing the plant for textile fiber) sequester carbon five to 10 times more effectively than wood. Wheat straw, for example, is 40 percent carbon, as measured by weight. These materials pose no health risks. They are insulative, acoustically absorptive, and, of course, rapidly renewable. Plus, using them for building components creates new markets for farmers.
Agrifibers just have a bit of an image issue. “The lack of awareness or misperception around the viability of the material may be the biggest barrier right now,” says Jacob Deva Racusin, director of sustainability and building science at New Frameworks, one of the conveners—along with MASS Design Group and Ha/f Climate Design—of a recent summit, held in Boston, with representatives from all along the bio-based materials value chain. “And that’s across all sectors, from practitioners to regulators to the market,” he says.
Starting to change perceptions around these materials are precedent-setting projects that demonstrate agrifiber’s suitability for 21st-century architecture. Outstanding examples include a pair of schools in Denmark, by Henning Larsen; an exhibition pavilion in the Netherlands, by Overtreders W (for Winnie-the-Pooh fans, that’s a reference in Dutch to Piglet’s grandfather); and two guest cabins in upstate New York, by youarethecity.
Sundby School and Feldballe School, designed by the Copenhagen-based Henning Larsen, each model a different application for bio-based materials—Sundby by innovating with a heritage craft in a contemporary building envelope and Feldballe pioneering a pre-fabricated system of straw-insulated structural panels. “The big achievement in these projects is that they combine doing good architecture with a biogenic response,” says Eva Ravnborg, project director at Henning Larsen. “They’re not compromising one or the other.”
Winner of a World Architecture Festival Award for Best Future School, the two-story, 91,000-square-foot Sundby School, designed in partnership with skala architecture and now nearing completion, is the first primary school in Denmark to earn the Nordic Swan Ecolabel. Located in the rural area of Lolland-Falster, in a low-income region of the country where children commonly grow up “with not necessarily the biggest sense of pride in where they come from,” Ravnborg says, the design aims to elevate students’ views of their place.
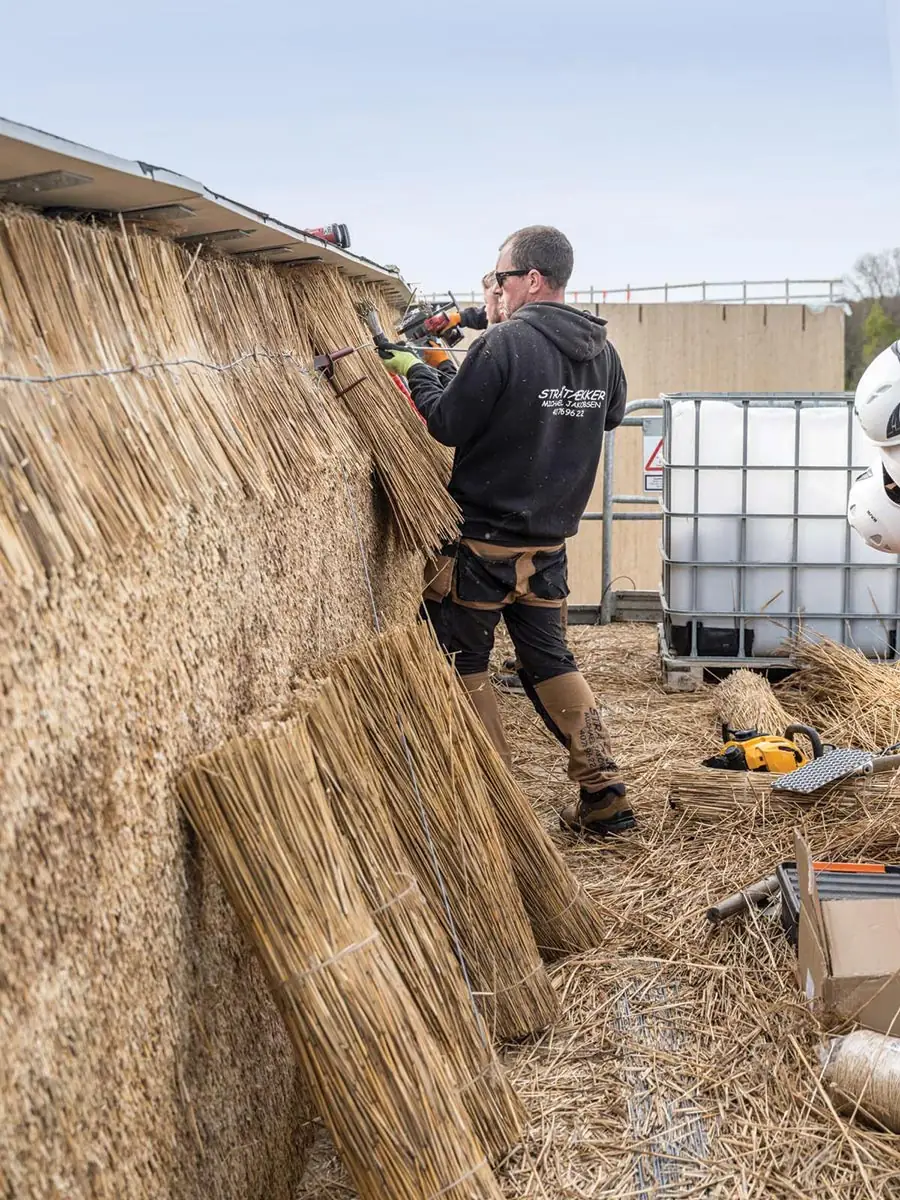
1

2
The outward-facing curve of the Sundby School (top of page), in Denmark, is clad in a nearly 10-inch-thick layer of thatch (1). The thatched facade (2) of the Sundby School (3) is expected to last 80 to 100 years. Photos © Rasmus Hjortshøj, click to enlarge.
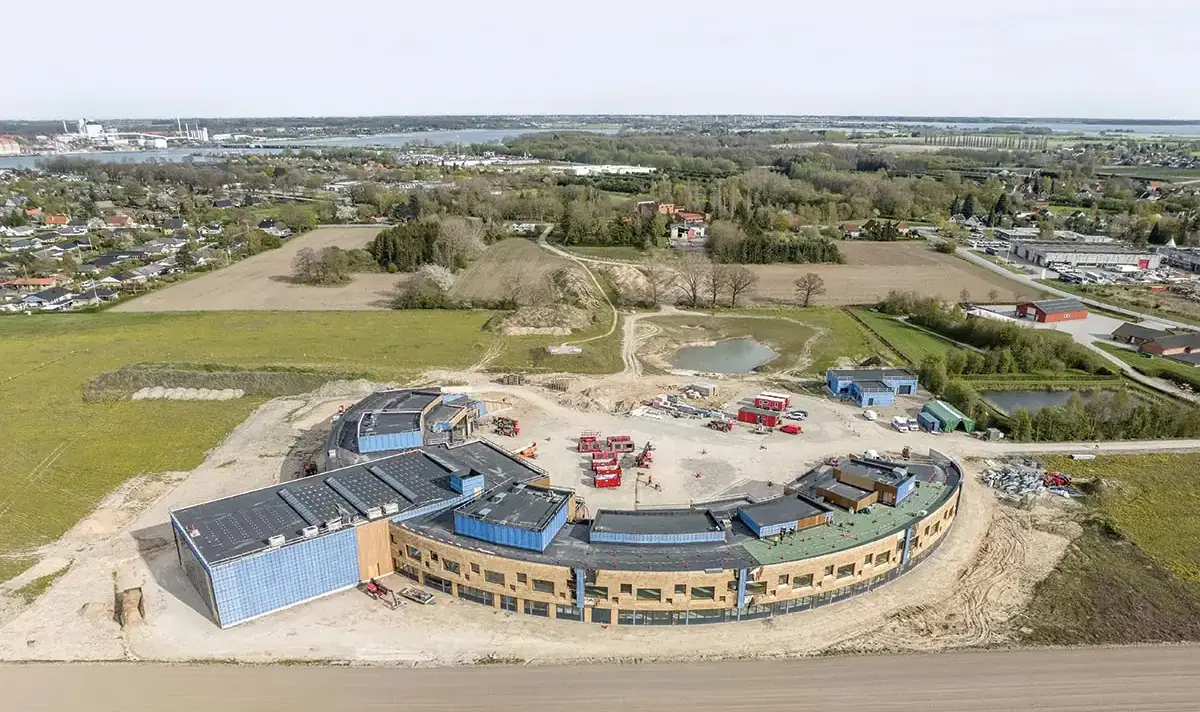
3
Semicircular in plan, the structure seems to push out of the earth “like a treasure,” Ravnborg says, referring to Viking artifacts found in the region, and offers the children expansive rooftop panoramas of their home landscape. Cladding the school’s outward-facing curve, as part of an otherwise-conventional envelope assembly, is a nearly 10-inch-thick layer of thatch (which will compress over time to about 8)—a millennia-old system of tightly bundled and layered reed or straw. Conveying a sense of warmth and protection from the region’s prevailing winds while augmenting the performance of the assembly beneath, the thatched facade is expected to last 80 to 100 years and can easily be repaired during that time if needed. “It’s very much a local facade reference that we are trying to rework and translate into a modern version,” says Per Ebbe Hansson, lead design architect at Henning Larsen. “Introducing this element in our design, we were able to reference local heritage and mirror the school’s surroundings, with the aim of uplifting both.”
The main challenge in the use of thatch was the need for increased scrutiny around fire safety. A costly year-long process of testing, including burning one-to-one mockups to study flame spread, temperature, and other factors, established that the design’s provisions for compartmentation, egress, and firefighting meet the applicable safety standards. “The problem is that this is very specific for this project,” Hansson says, “so if you want to do a similar project, we have to start all over again.”
Where Sundby School showcases bio-based materials in a distinctive and expressive work, the architect’s 2,700-square-foot extension to Feldballe School, in Rønde, completed in 2022 on what Ravnborg describes as “almost no budget,” serves as a test case for prefabricated modular wood-framed panels stuffed with compressed straw. “This is a project with which we tried to say, ‘Every solution we create here, we need to be able to scale up,’” she tells RECORD. “‘We need to imagine that this is able to grow and become a much larger project.’”
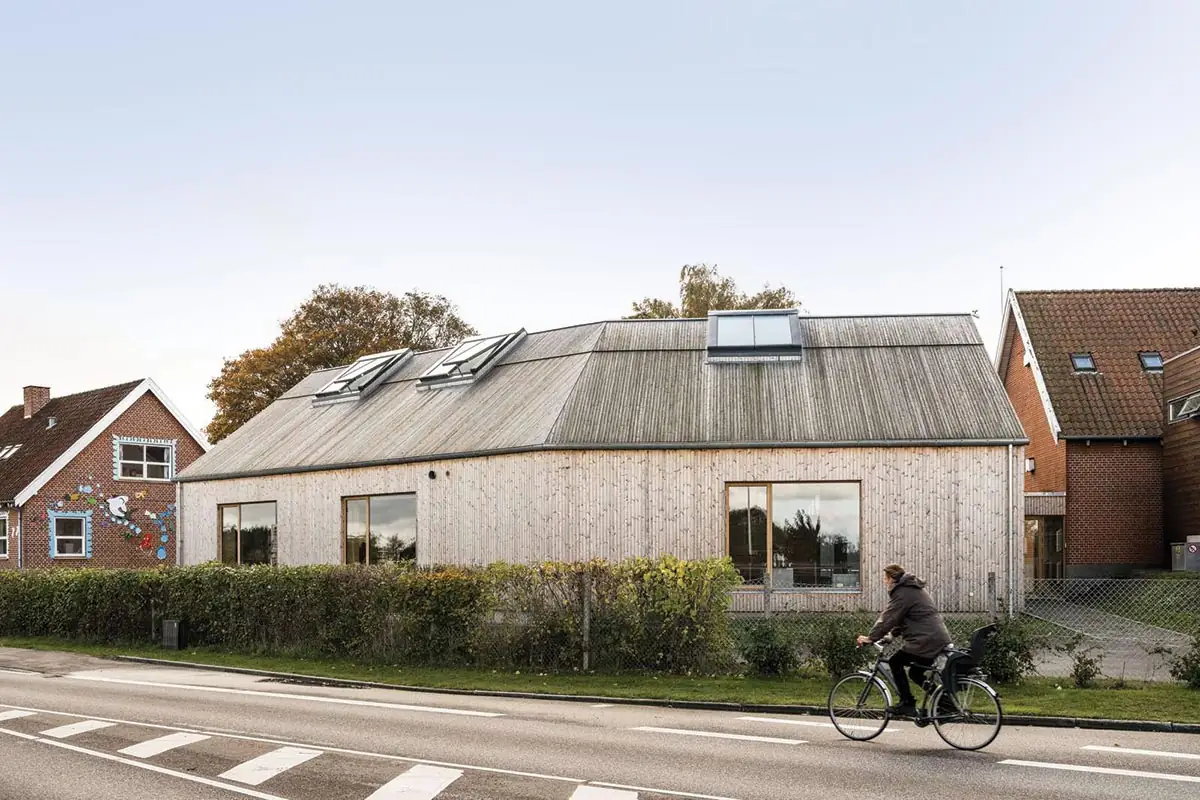
4
An extension to the Feldballe School, in Denmark, features panels that are wood on the exterior (4), clay plaster on the inside (5), and stuffed with compressed straw. Photos © Rasmus Hjortshøj (4), Helene Høyer Mikkelsen (5)
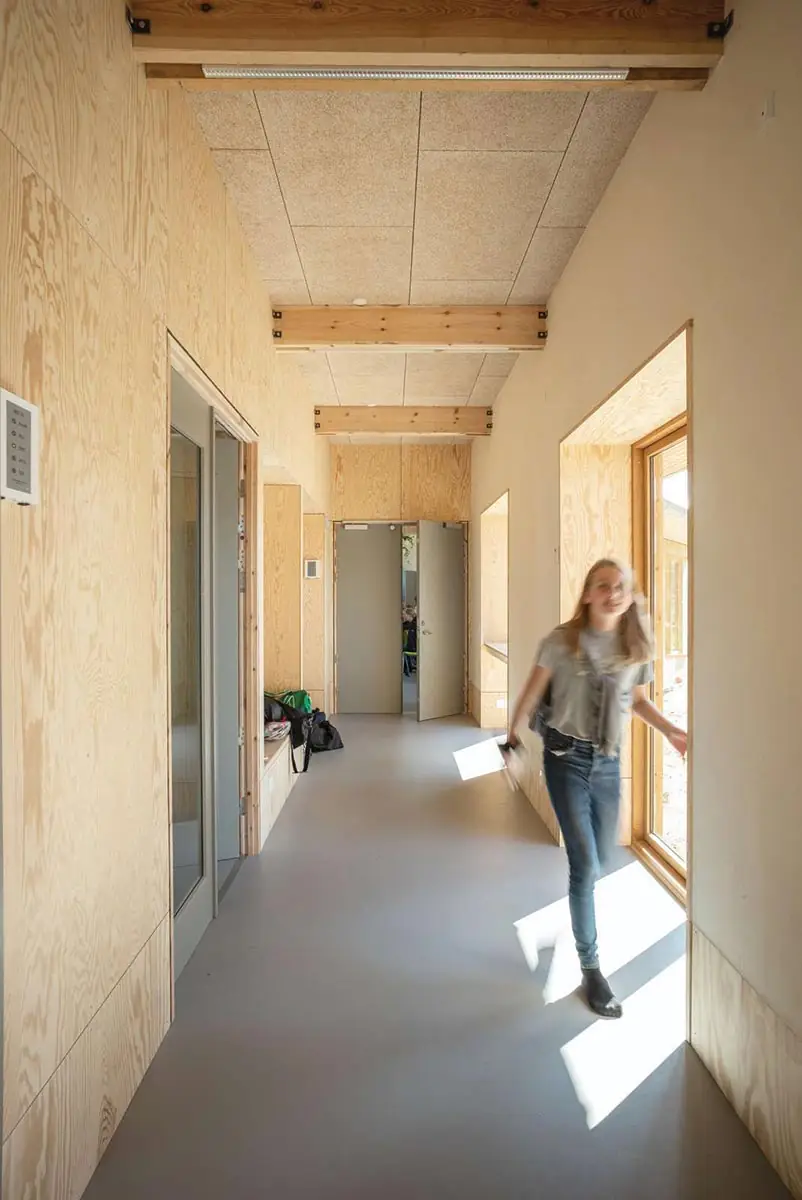
5
Unlike Sundby School’s magnificent thatched facade, the structural panels did not require skilled heritage-craft workers, and went up in a day. The panels are clad on the outside with wood and on the inside with a clay plaster, which serves as a vapor-permeable membrane allowing the straw to “breathe.” The structural insulated panels (SIPs) are about a foot and a half deep (providing insulation in the range of R-35) and, together with their finishes, make for walls approaching 2 feet thick. “Suddenly, there’s a different type of architectural vocabulary that comes with the greater facade depth,” says Ravnborg. Windowsills, for example, where a child can sit, so “it’s not necessarily just a disadvantage.”
Densely packed straw burns poorly, in a manner similar to heavy timber, and the structural performance of the panels compares to light-frame wood. As a manufactured product, the SIPs came pre-tested for fire and structural performance. A critical design focus was detailing the wall to prevent moisture ingress; a removable panel along the base of the wall provides access for monitoring (as well as incorporating a cable run). Because the whole building is designed for disassembly, if a panel were to become damaged, it could be switched out. “The idea is that it’s not going to be necessary, but it is theoretically possible,” says Hansson, “and at the end of the life of the building, the entire thing can be disassembled and reused.”
Although small, the Feldballe School is having a big impact. Henning Larsen is now designing a 1.7 million-square-foot logistics center in the Netherlands using the same system of straw-insulated structural panels. “So it is going from a very, very tiny project to an extreme scale-up,” says Ravnborg, “but that is only possible because we could bring the client to see and touch this project and get a sense of it. That is really convincing.”
Showcasing the potential of bio-based materials was equally central to the brief for the Voice of Urban Nature, a pavilion designed by Amsterdam-based Overtreders W on the theme of greening the future city. Commissioned jointly by the neighboring municipalities of Amsterdam and Almere for the Netherlands’ decennial horticulture exposition, Floriade, in 2022, the pavilion contains six gardens (designed by Joost Emmerik and De Onkruidenier) and an exhibition (by architect Kossmanndejong), each exemplifying the variety and potential of urban nature.
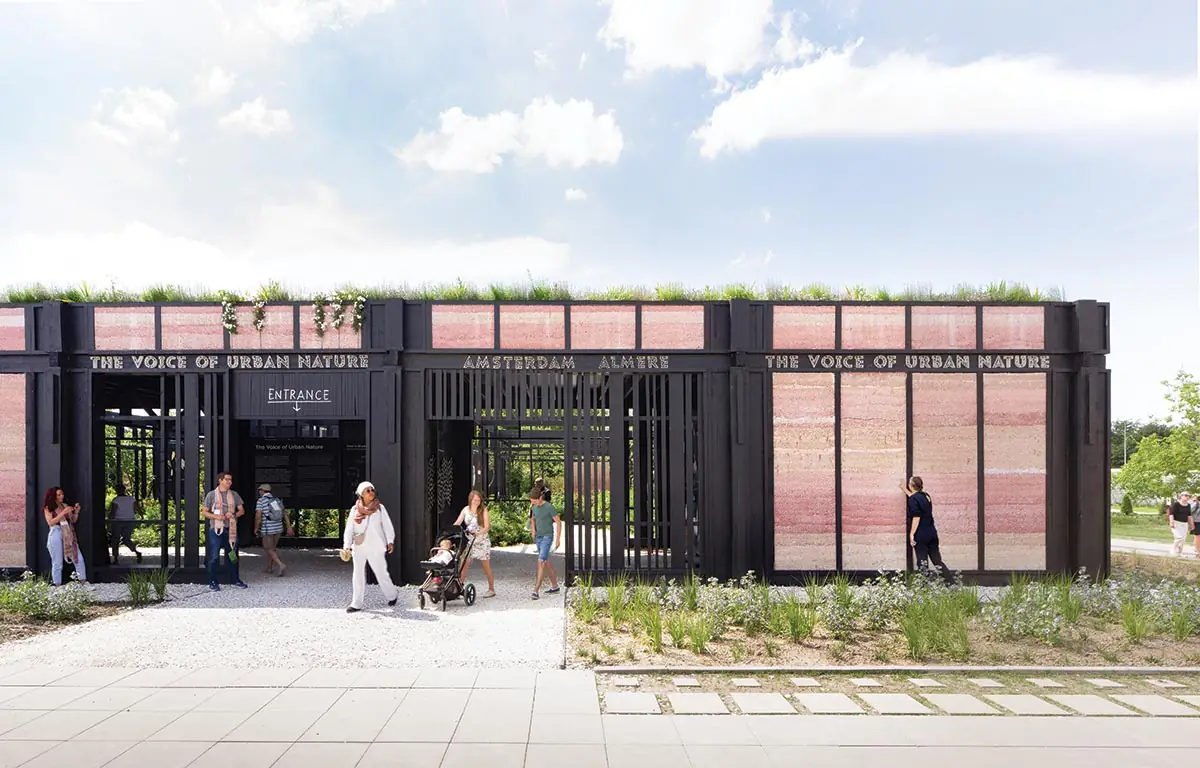
A pavilion for the 2022 Netherlands’ decennial exposition, Floriade, pilots modular demountable hemp-lime panels. Image © Pano Bewerkt
In designing the structure, “the most important thing for us was to show a new aesthetic of bio-based building—to not make it beige, but more fresh and ‘nowadays,’” says Reinder Bakker, a partner at Overtreders W. “And, because bio-based buildings are often thought of as mainly for the countryside, we also wanted to show these materials can work in a city.”
The pavilion’s structure pilots an Overtreders W–designed system of modular, demountable, wood-framed hemp-lime panels in rosy shades of pink. Sometimes known as hempcrete (a misleading term that seems to imply concrete-like structural properties, which the material does not have), hemp lime consists of hemp hurd mixed with lime powder and water. The pavilion’s hemp comes from a nearby farm, and its lime from neighboring Belgium, while dye from regionally grown madder is what gives the panels their color. “There’s already a lot of research and knowledge about hempcrete, so it’s not a new material,” Bakker says. As well as being carbon-negative, insulative, and acoustically absorptive, hemp lime has proven naturally resistant to pests, mold, and fire, requires very little energy to produce, and can be fully recycled or safely returned to nature as part of a zero-waste economy. “But—as well as with the aesthetics—we tried to do a bit of a new thing with prefabricating, so the quality control is better, it can be cheaper, and, if it’s raining outside while they’re making the panels, it’s not a problem.”
Supporting the panels is a timber structure (also modular and demountable) built from demolition salvage and trees felled in managing local nature reserves. The wood is stained black using carbon-infused linseed oil from flax grown at Amsterdam’s Schiphol Airport (to deter geese, who don’t like flax, from getting accidentally involved with the planes) and pressed at a windmill outside the city.
Through its designs for experimental temporary buildings, Overtreders W aims to advance a more circular economy for building materials—because ultimately, Bakker says, “all buildings are temporary.” The Voice of Urban Nature’s hemp-lime panels have attracted a lot of interest, and Overtreders W considered starting a new company to manufacture the product commercially (as they did for a recycled-PVC-tile cladding that they developed for a previous project), “but we are ultimately designers and architects,” Bakker says. So instead of launching another enterprise, the firm is using its modular hemp-lime panels in a new building, a retreat center starting construction this year, “to show that it’s possible in a more permanent project,” Bakker says.
In the U.S., building products based on both straw and hemp are becoming increasingly available. Straw-insulated structural panels, similar to those used in Feldballe School, are manufactured in varying thicknesses in a growing number of regions, and, as Henning Larsen’s experience suggests, that product is ripe for scaling up. Hemp farming was legalized in this country in 2018 (after more than 70 years of prohibition) and hemp lime was approved as a residential building material in 2022, so that market is still in its infancy here. “It’s just a number of years until it will happen, but it does need to be prioritized at a societal level, as well as individuals’ chipping away at it,” says Kaja Kühl, founder of the Brooklyn-based urban design and research practice youarethecity, and the designer, with New York–based Roger Cardinal Design, of two micro dwellings built in 2022 with hemp lime.
Located at Wally Farms, a 1,000-acre experimental-farming and climate-research incubator in New York State’s Hudson Valley, each cabin is less than 400 square feet and opens to the landscape with wide sliding doors. Designed in consultation with contractor Hempstone, the structures’ walls consist of light-wood framing. They are lined with a continuous inner layer of insulative hemp-lime blocks, prefabricated in Pennsylvania. Between the studs is a 7-inch layer of site-mixed spray-on hemp lime, from France, where the material has been used for decades in restorations and more recently in new multistory construction. Even factoring in transportation emissions, the hemp lime is still carbon negative. The combination of the two formats enabled work on the interior finish, a vapor-permeable lime plaster that also acts as an air barrier, to go ahead while the spray-on product dried. The structure was then wrapped with an additional layer of wood fiberboard insulation and a rainscreen cladding of cedar shingles.
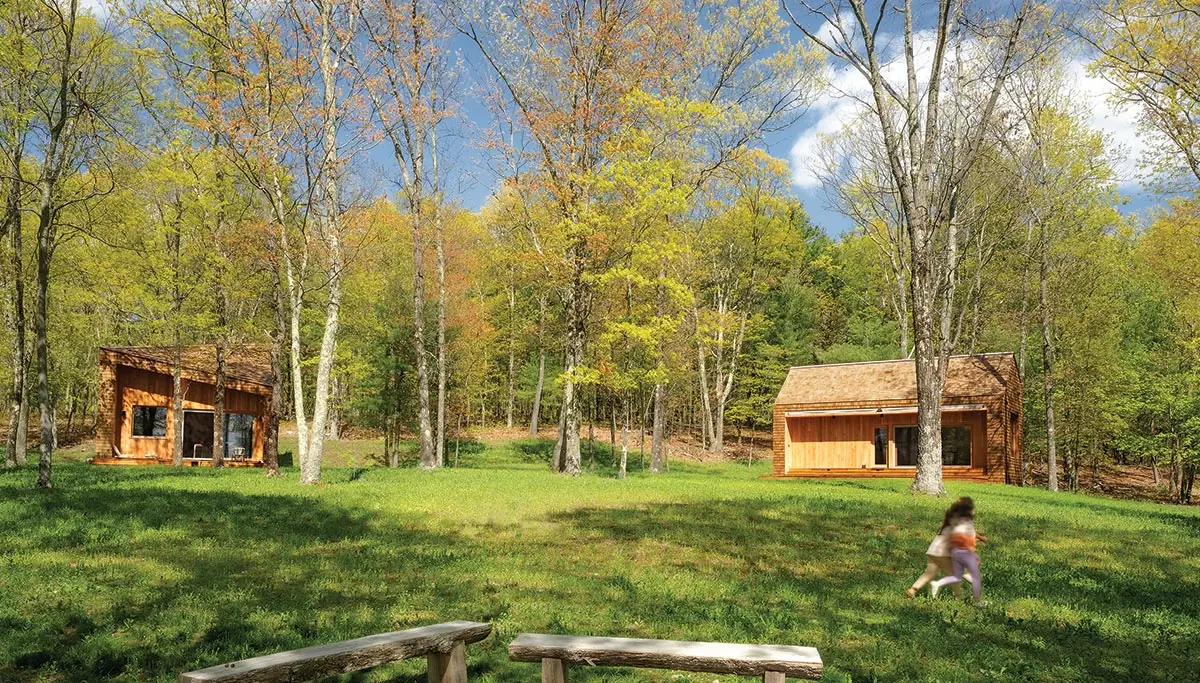
6
A pair of wood-frame cabins (6 - 8) in New York State’s Hudson Valley uses hemp lime in prefabricated blocks and in a spray-on format. Photos © Laslo Kovacs (6 & 8); Hempstone (7)
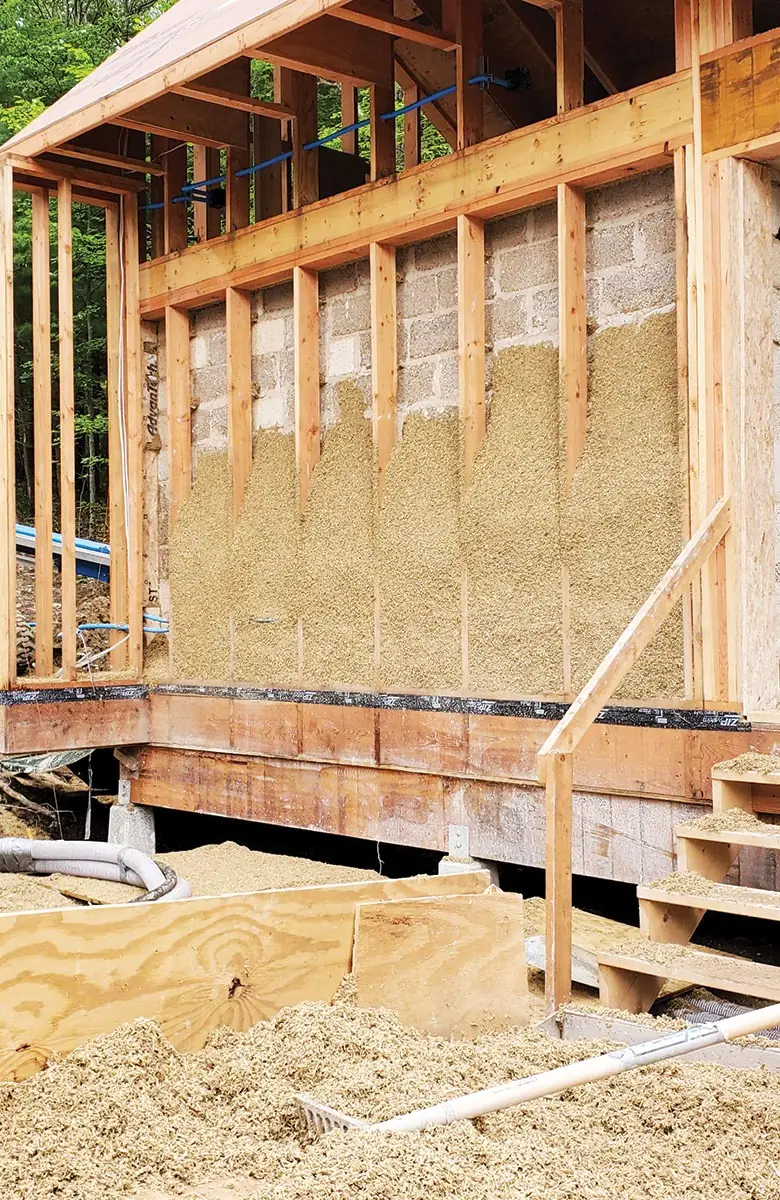
7
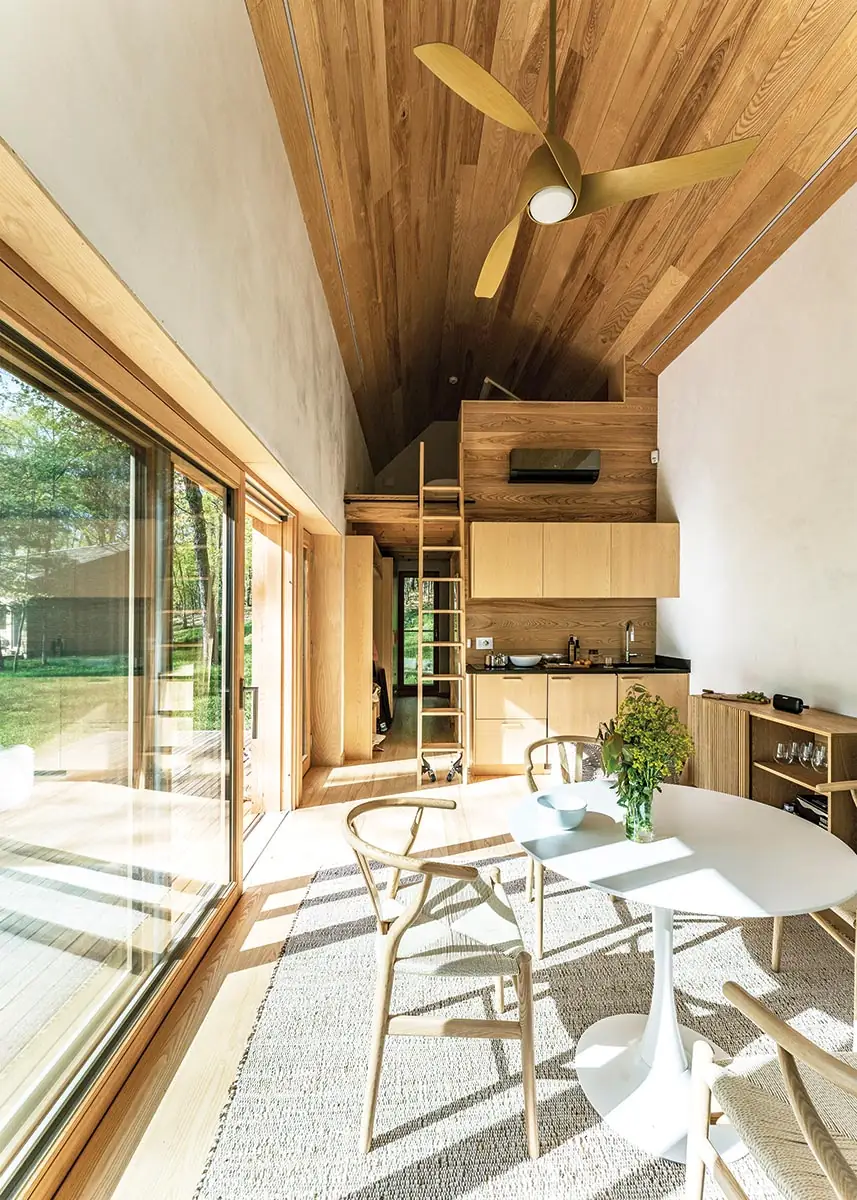
8
To estimate the buildings’ embodied-carbon emissions, the project team used BEAM (Building Emissions Accounting for Materials), a carbon calculator developed by Builders for Climate Action and one of the few tools that includes the carbon stored in biogenic materials (other than wood). The cabins’ embodied carbon totaled about 1.7 metric tons, an approximately 90 percent reduction per square foot from typical construction. The concrete foundation and, to a much lesser degree, the windows account for almost all of it, “a great illustration of just how carbon-intensive concrete is,” Kühl says.
Since the completion of the guest cabins, Wally Farms has continued to advocate for hemp as a healthy, regenerative construction material—that also creates green, rural jobs—by offering site tours and on-site workshops for designers, builders, farmers, and real-estate professionals. As an additional resource, an online project diary documented the research behind the project.
These path-breaking projects, along with a growing number of others, provide valuable precedents for changing the perception of agriculture-based materials in contemporary architecture. What’s needed next, according to the Boston conference proceedings, are more data on these materials’ properties, behaviors, and impacts; policies and codes that facilitate their wider uptake; and initiatives to support industry and supply chain development.
Continuing Education

To earn one AIA learning unit (LU), including one hour of health, safety, and welfare (HSW) credit, read the article above and United Nations Environment Programme (2023). Building Materials and the Climate: Constructing a New Future. Nairobi. Chapter 4, “Shift to Bio-Based Building Materials,” pages 27 – 40. Then complete the quiz.
Upon passing the quiz, you will receive a certificate of completion, and your credit will be automatically reported to the AIA. Additional information regarding credit-reporting and continuing-education requirements can be found at continuingeducation.bnpmedia.com.
Learning Objectives
- Discuss the health and environmental impacts of conventional manufactured building materials.
- Explain the carbon-storage properties and circularconstruction potential of agriculture-based building materials.
- Describe ways agriculture-based materials can be used in prefabricated and modular systems.
- Describe structural and fire-resistance properties of various bio-based materials and assemblies.
AIA/CES Course #K2407A