The building industry has a waste problem. According to the Ellen MacArthur Foundation, a British nonprofit focused on accelerating the transition to a circular economy, upward of 50 percent of demolition-materials waste ends up in landfills. It is a great squandering of financial and materials resources and their associated embodied carbon, with the manufacture of steel and cement alone accounting for over 15 percent of annual global emissions. But there is an alternative path, through the reuse and recycling of building materials in a process dubbed circular construction. That practice is nothing new; the Romans even had a term for it, spolia, for the stone elements taken from old structures and reused for structural or decorative applications. Matters are more complicated in the modern age, with fine-tuned building systems and rigorous codes; and, with global supply chains geared toward take-make-waste (or linear) models, optimal logistical infrastructures to deliver circular-construction projects at scale are often lacking. However, designers and educators are exploring different avenues to utilize these mountains of debris, and are developing design strategies to reduce waste in the first place, such as adaptive reuse and design for longevity or for ease of disassembly.
Arup, the global engineering giant, is no stranger to developing novel solutions for seemingly intractable problems. In 2022, the firm, in collaboration with the Ellen MacArthur Foundation, launched the Circular Building Toolkit, which offers designers a comprehensive framework to reduce the use of virgin and nonrenewable products and improve material efficiency, among other strategies. For Arup Americas chair Fiona Cousins, the Toolkit is also an open-access platform that helps architects, and the overall construction market, differentiate between the subject of circular construction, which focuses on where materials come from and where they are going, and the larger conversation of embodied carbon and how materials are made.
A framework is only as good as its implementation, and Arup is rolling out practices outlined in the Toolkit, such as material passports, which log information about materials, products, and components, within BIM models, across a range of projects. Notably, according to Frances Yang, Arup associate and leader of its sustainable-materials practice in the Americas, the firm focuses those efforts toward high-value or higher-churn building components, like ceiling tiles and door systems, where greater impact can be had. “Overall, we realized that you need to be strategic about the documentation, and to avoid an all-or-nothing approach that is daunting for clients and burdensome in terms of data collection.”
London has emerged as a testing ground for putting these ideas into practice owing to the city’s rollout in 2022 of mandatory circular-construction guidelines (preceded by a set of voluntary instructions in 2019). The regulations require whole-life-cycle carbon assessment and circular-economy statements to receive planning approval for large buildings, with the aim of furthering London’s goal to reach net zero emissions by 2030 through discouraging demolition and encouraging reuse. One Triton Square, a commercial building designed by Arup and completed in 1998 as the First National Bank of Chicago’s London outpost, now follows these principles, having wrapped up an all-encompassing retrofit at the tail end of 2021. The retrofit of the limestone-and-glass-clad concrete building was also led by Arup, for developer British Land, which committed to a circular approach to the project. It helped that Arup kept drawings of the building’s original systems and materials, reducing the cost and time associated with development of a digital twin BIM model from an entirely new building survey.
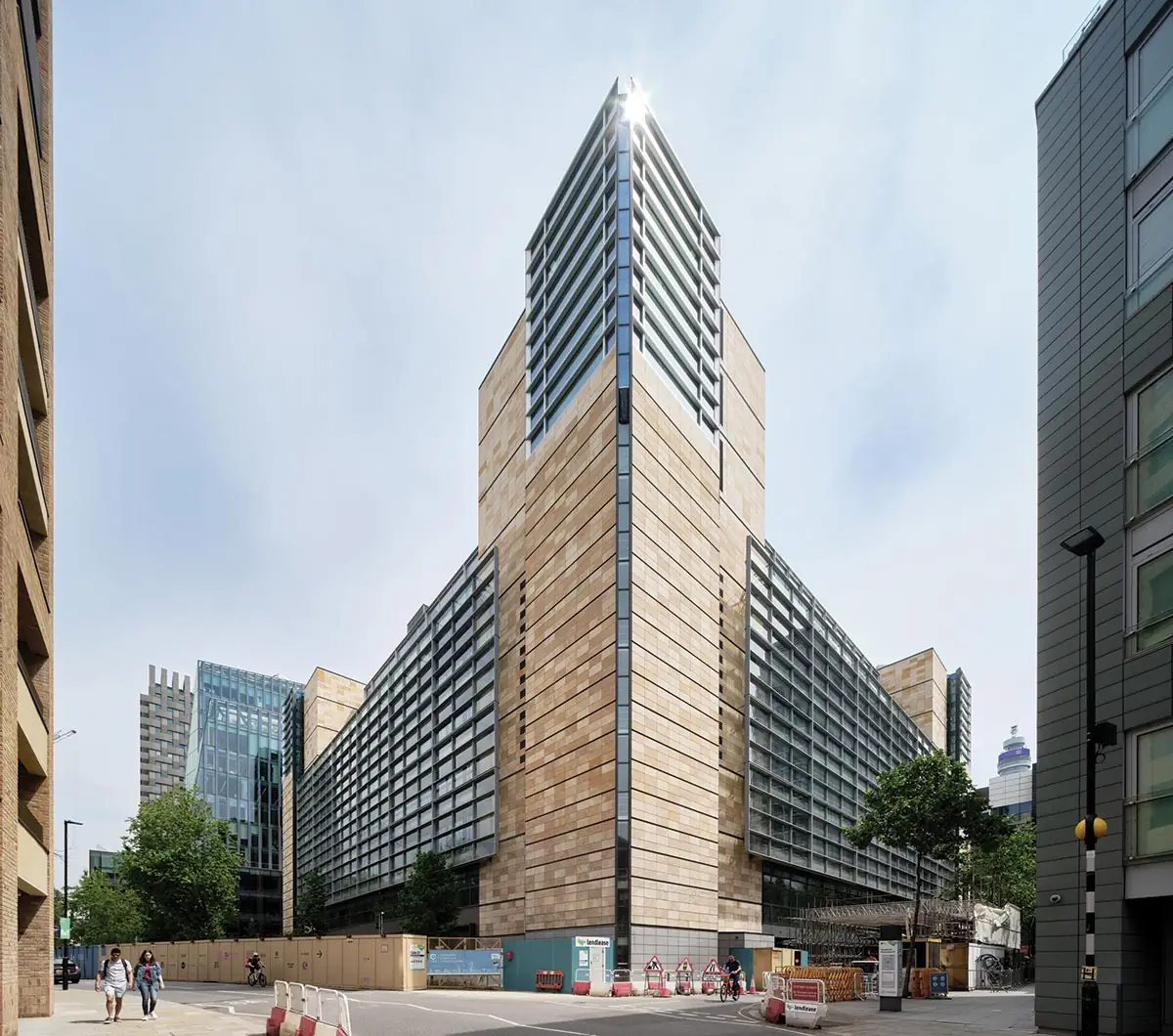
1

2
One Triton Square, in London, was originally designed by Arup in the 1990s, and the firm led its comprehensive retrofit more than two decades later (1). The curtain wall was disassembled and refurbished at a temporary fabrication site in the metropolitan region (2). Photos © Simon Kennedy, click to enlarge.
The redevelopment of 1 Triton Square included the addition of three stories to the existing six, with substantial expansions to the floor plate within the building’s atrium. The design team supported the additional load by expanding the diameter of the structural columns from 8 to 10 inches and, in several circumstances, wrapped them in fiber-reinforced polymer for further strengthening. At the exterior, the original aluminum-and-glass curtain wall system was disassembled, and was refurbished with new gaskets and glass coatings, for greater thermal efficiency, at a pop-up factory less than 30 miles away, and reinstalled. For new construction, the design team sourced lower-carbon cement replacements (blast furnace slag makes up 70 percent of binder used for the concrete) and successfully integrated updated mechanical infrastructure within previously allotted m/e/p channels. In total, the retrofit of 1 Triton Square saved some 35,000 tons of concrete and nearly 2,000 tons of steel that, with additional measures, translated to 40,000 tons in carbon dioxide savings—while, at the same time, reducing the project budget and construction schedule as compared to new construction.
GXN, a research studio founded by Danish architecture firm 3XN in 2007, is also leading the way in circular construction, with several projects on that model in London. The group, which works with its parent firm, recently received planning approval for The Mark, an approximately 320,000-square-foot commercial project that will combine four existing buildings into a single entity. “We are increasingly working in London around these new policies, and, in advising clients, we help determine which materials they should focus on and how they can use them in their own scheme, or in others,” says Kåre Stokholm Poulsgaard, GXN partner and head of innovation. “A large part of this is developing the workflows that align with the needs of the client, the contractor, the cost consultant, and the material conveyer. What kills off circular projects are the unknowns.”

3
The Mark will consolidate and build over existing buildings a few blocks from the Tower of London (3); GXN scanned the buildings to produce digital models (4). The Mark has been soft-stripped of materials like raised access floors and carpet tiles (5). Images © 3XN GXN

4

5
Work began in May 2022 with a pre-demolition audit using Matterport, a 3D-mapping application, which informed, with the help of their own in-house software, the design team’s identification of areas for the greatest reuse and recycling potential. Soft stripping, or the removal of nonstructural elements, began in early 2024 with such items as raised-access flooring, and ceiling and carpet tiles, among others, offered on the Excess Materials Exchange, a digital platform for salvaged materials; the design team’s aim is for most of those items to be reused on other London construction sites. In addition to maintaining some of the structural systems, they are also investigating the reuse of materials found on-site for new purposes, such as placing the original stone facade as flooring in the front-of-house areas.
Click diagram to enlarge

Image © 3XN GXN
London is not alone in its attempt to become a global circular-construction hub. This year, the New York City Economic Development Corporation (NYCEDC) launched its own circular-design guidelines, to be implemented across its expansive $9 billion portfolio of capital projects starting in 2024. The guidelines are ambitious and aim for a 50 percent reduction in embodied carbon, largely through circular practices, such as reducing construction, and deconstruction material for disposal, by 75 percent; reusing or recycling 95 percent of concrete and soil generated by either construction or deconstruction for highest-use value; and for 25 percent of all virgin materials used to be low-carbon, such as mass timber. The goal, according to NYCEDC’s chief strategy officer Cecilia Kushner, is not only to support New York’s green transition, but to harness the economic heft of the NYCEDC to engender a larger market of circular construction for private actors across the city.
The Science Park and Research Campus (SPARC), in the Manhattan neighborhood of Kips Bay, will serve as a five-acre laboratory for the NYCEDC’s guidelines. The 2 million-square-foot project, to be designed by Ennead and Dattner Architects, with engineering services by Buro Happold and LERA and master-planning by SOM, will replace the existing Hunter College Brookdale Campus. The design team was awarded the project in March 2024 and, at this nascent stage, has not developed a completed scheme for SPARC Kips Bay, though the existing-building survey, with digital scans, has commenced. With that information in hand, the team will do an audit to best determine the project’s circular-construction opportunities and begin deconstruction during summer 2025. Construction is scheduled to begin by 2026 and should be complete in 2031.

SPARC Kips Bay is a full-block site. Photo © SOM
Click diagram to enlarge
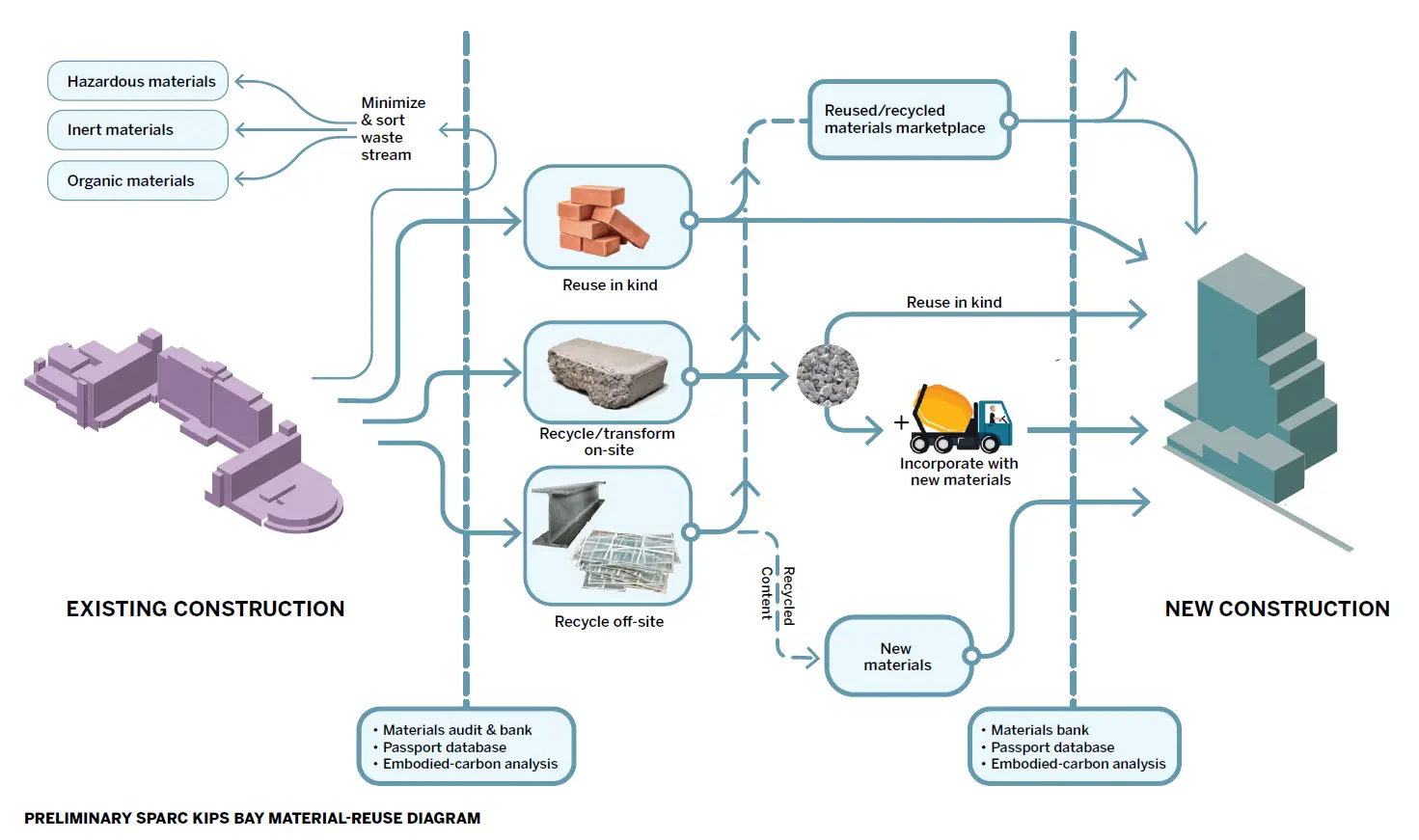
Image © Ennead & Datter
There are also opportunities to be had in harnessing dismantled-building components for new construction, should a more robust marketplace and the related infrastructure be developed. ETH Zurich’s Circular Engineering for Architecture (CEA) lab, founded in 2021 and led by Catherine De Wolf, is making advances in that area. According to De Wolf, as it stands, circular construction is mainly confined to large but niche projects, such as The Mark or the renovation of Centre Pompidou, where De Wolf led a team that salvaged the structure’s distinctive curved glass panels for use as office partitions. In many circumstances, it is limited by the ambitions of individual clients, and greater subscription by the construction sector requires the build-out of an entirely new marketplace, one that can match salvaged materials to the broad specifications of individual projects. De Wolf’s interdisciplinary team, ranging from experts in civil engineering to industrial ecology, is attempting to do just that, using AI-powered software. “Anyone involved in material reuse currently has to know and source from local retailers, find the appropriate storage facilities, and have knowledge of which platforms to look into, and then screen all of them to find suitable materials for their project,” notes De Wolf. “What we are trying to do is create a matchmaking service, not unlike dating apps, between people who have materials available for reuse and buyers, developers and skilled workers familiar with disassembly and reassembly, and other services within circular construction.”
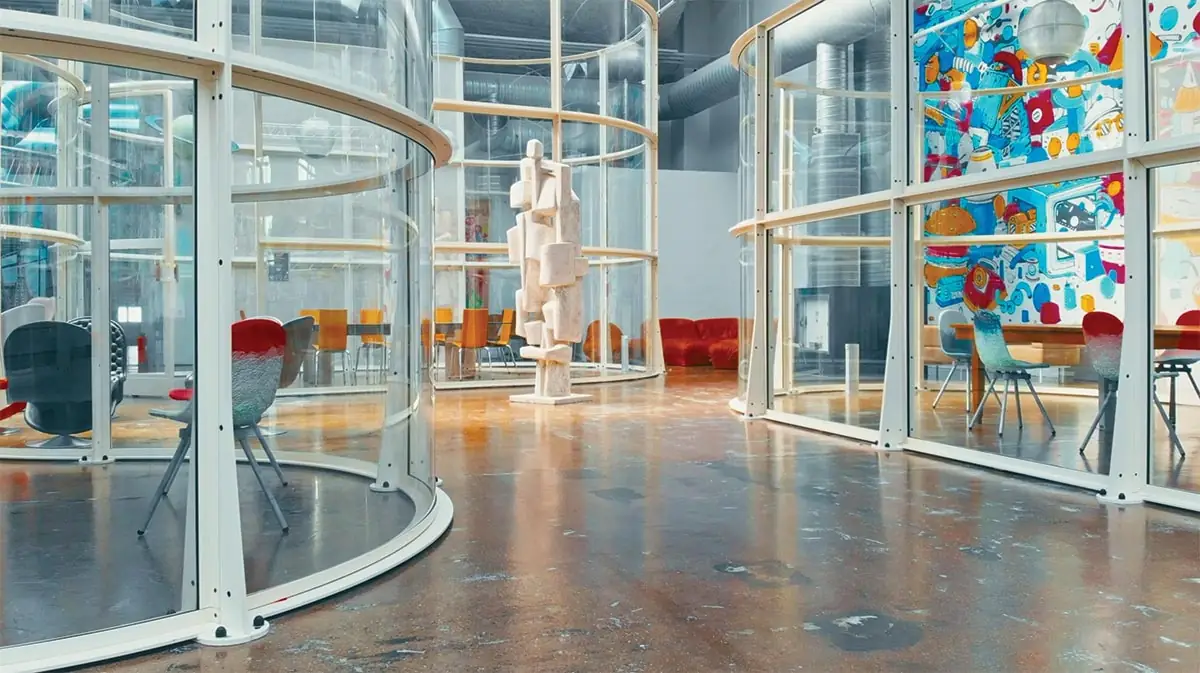
The Centre Pompidou’s curved glass panels were reused as office partitions. Photo © Maximum Architecture / Alexandra Attias

A mock-up built of wood for a castaway-brick pavilion. Photo © KVA MATX
In Cambridge, Massachusetts, MIT School of Architecture’s Spoon Climate Studio, led by professors Sheila Kennedy and Caitlin Mueller, is probing similar questions. “There has been such an emphasis on standardization and uniformity of materials in Modernism, and we have inherited those assumptions on their benefits,” notes Kennedy. “But we’re beginning to see the end of that particular regime, certainly in terms of supply-chain problems, and in terms of the cost of extracting new material resources and delivering them to new building sites.” The Studio’s Odds & Mods course probes that paradigm by sourcing waste streams from different factories across North America—mainly bricks—for students to develop into architectural prototypes that reflect the inventories and stockpiles available in specific locales. Notably, according to Kennedy and Mueller, the initiative has received enthusiastic buy-in from domestic brick manufacturers like Glen-Gery and Morin Brick and, farther afield, from some in Mexico’s Volcanic Belt. They otherwise are impelled to discard up to 15 percent of their production due to slight imperfections, such as being the wrong color.
Click diagram to enlarge

Image © KVA MATX
It is, of course, preferable to stem the creation of those waste streams in the first place, and, to that end, Mueller is leading a team of researchers—Keith Lee, Pitipat Wongsittikan, Jenna Schnitzler, and Inge Donovan—in collaboration with manufacturer Holcim and the real-estate investment trust Prologis—to develop design and computation strategies to allow concrete building elements to be disassembled and rebuilt multiple times. The post-tensioned system called PixelFrame uses concave concrete modules of varied strength, sans rebar. They slide onto a central steel core without the need for grout or mortar, which often poses an obstacle to reusability. According to Mueller, the PixelFrame system allows for more than 50 percent up-front embodied-carbon savings as compared to traditional reinforced concrete, which compounds further with each additional reuse.

5

6
The PixelFrame system is modular (5), and can be used for columns and beams (6). Photos © Inge Donovan and Jenna Schnitzler
On a larger scale, the shift away from uniformity and toward diversity in design could look like the 3XN-GXN-designed Tscherninghuset in Hedehusene, Denmark. The approximately 180,000-square-foot interior project is, fittingly, the new headquarters for Tscherning, a demolition company. The design team sourced nearly 90 percent of the materials, including recycled concrete slabs and aggregate for load-bearing walls and decks, from the client’s many building sites. Within, a panoply of finishes, from charred wood to terra-cotta shingles and reclaimed brick, renders something of a village-like environment, albeit for corporate programming.

The Tscherninghuset incorporates a multitude of recycled materials. Photo © Claus Peuckert
While there is an abundance of construction materials available for reuse, the building industry, and society, is in a race against time to reduce carbon emissions. As outlined by the 2015 Paris Agreement, greenhouse gas emissions must be reduced by 45 percent by 2030, and net zero must be reached by 2050, to avoid global warming’s worst impacts. The tools and techniques are steadily developing to advance circular construction as a potent instrument to address the building industry’s complicity in the climate crisis. But, at the end of the day, the road to less-wasteful construction may be through legislation, providing regulations for procurement of reused materials and mandating building deconstruction rather than demolition. In order to have a circular economy, advises Arup’s Cousins, “you have to make the link between the beginning and the end.”
Continuing Education

To earn one AIA learning unit (LU), including one hour of health, safety, and welfare (HSW) credit, read the article above and Clean and Circular: Design & Construction Guidelines, NYCEDC, version 1.0 (through page 13). Then complete the quiz.
Upon passing the quiz, you will receive a certificate of completion, and your credit will be automatically reported to the AIA. Additional information regarding credit-reporting and continuing-education requirements can be found at continuingeducation.bnpmedia.com.
Learning Objectives
- Understand the role of construction in carbon pollution and explain how circular practices can reduce such emissions.
- Describe strategies for the reuse of numerous materials, including structural and enclosure components and finishes.
- Identify policy decisions that could further develop the marketplace for circular construction.
- Explore emerging software applications that aim to support circular construction.
AIA/CES Course #K2406A