Design-Build Giant Katerra Acquires Lord Aeck Sargent, Michael Green Architecture
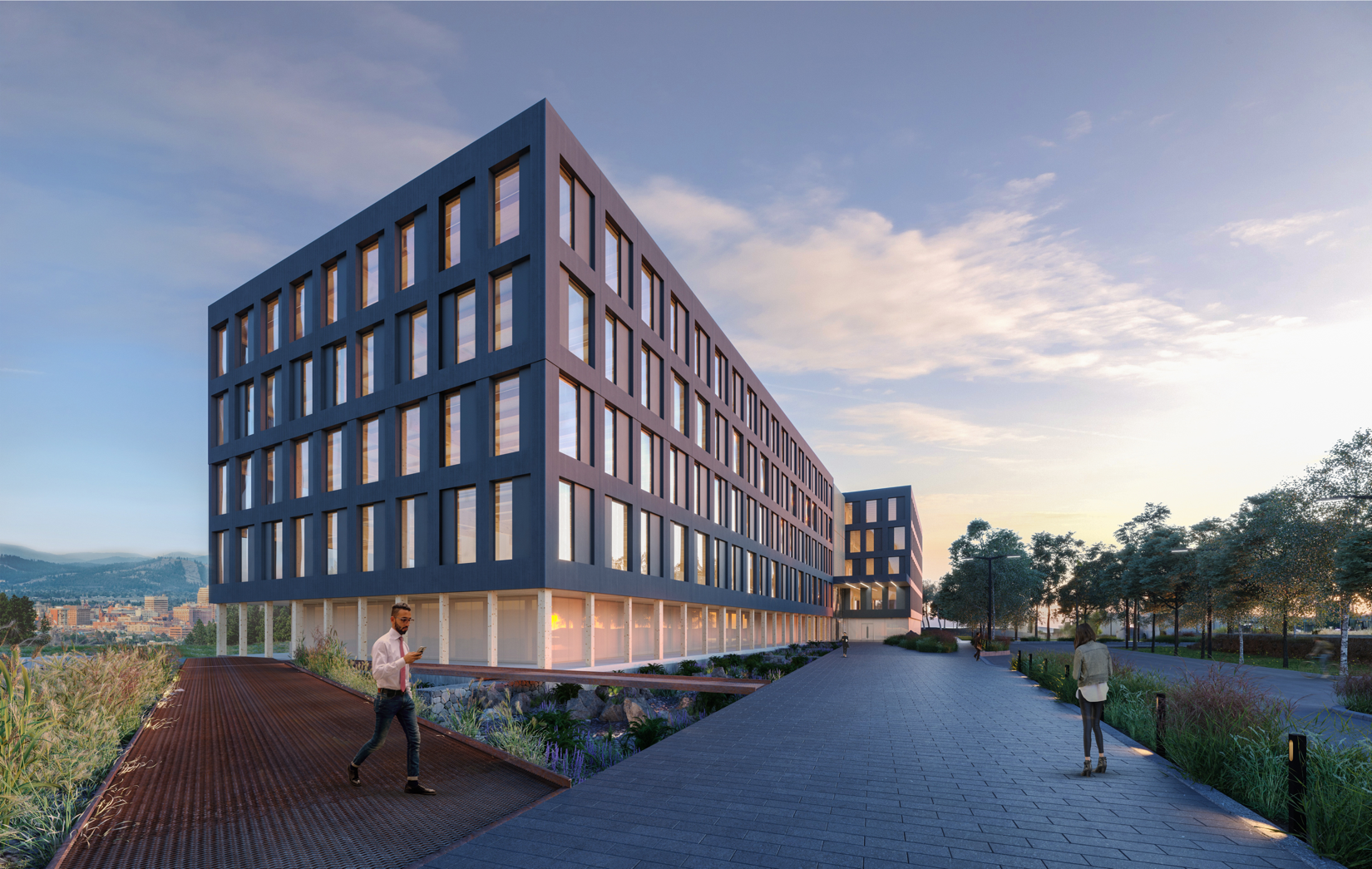
The 150,000-square-foot Catalyst Building in Spokane, Washington, will be the state's first office building constructed of cross-laminated timber. It will also be connected to an energy resource sharing "eco-district" planned for the development.
Rendering courtesy Katerra
Architects & Firms
In three short years, the design-build firm Katerra has grown from a Silicon Valley entrepreneur’s bright idea into what could become one of the largest commercial/residential design-build firms in the country. The strategy: vertically integrate every layer of construction, from architecture to the fixtures and subcontracting, in order to lower costs, build faster, and raise quality. The means: venture capital (over $1 billion so far) plus acquisitions of existing companies in the building and products industry.
Now Katerra is moving to buy architecture firms. In May, it acquired the mass timber innovator Michael Green Architecture of Vancouver, with a staff of 25. And as of today, Lord Aeck Sargent has joined Katerra’s ranks with 160 people and six offices sprinkled from Atlanta to Ann Arbor, Michigan. The two mergers offer insights into the depth and breadth of Katerra’s strategy.
“Michael Green and his team have built a reputation for engaging design and leadership in the use of mass timber,” said Michael Marks, chairman and cofounder of Katerra. “This goes a long way to support our mission to utilize cutting-edge technology and systems to revolutionize the construction industry.”
Said Katerra design director Craig Curtis, FAIA, of Lord Aeck Sargent, “It has a body of work that goes back decades and a deep bench of talent. And being able to deliver from the eastern time zone will be huge.”
Marks, the former head of Flex and interim CEO of Tesla, started Katerra in 2015 with Fritz Wolff, chairman of the real-estate development firm Wolff Company, and Jim Davidson, one of the founders of the venture firm Silver Lake. Headquartered in Menlo Park, California, the company has grown at an awe-inspiring pace courtesy of injections of capital, most notably $865 million in January from Japanese venture giant SoftBank. Since arriving in January 2016, Curtis, a 30-year veteran of Miller Hull, has built Katerra’s Seattle office into a team of some 100 architects and industrial designers. Further elements include a 200,000-square-foot factory in Phoenix, supplying wall systems, trusses, cabinetry, and fixtures. Katerra also operates a lighting factory in Shenzhen, China, and design and software-development offices in Pune and Bangor, India. In the last year, it bought two regional multi-family giants: Dallas-based residential remodeler United Renovations and northeast builder Fields Construction. Early next year, it will complete a 200,000 square foot CLT factory in Spokane. They have 19 projects under construction and dozens more in design, with reported billings of $1.3 billion. Still more acquisitions are planned. “We’re just Silicon Valley tech guys attacking an industry that hasn’t had any technology applied to it,” Marks said.
Katerra has focused on market-rate multi-family housing, student and senior living, and master-planned apartment developments for Wolff, supplying everything from integrated wall systems to cabinetry and fixtures. But Marks and Curtis take pains to distinguish Katerra as a “design first” design-build company. “We are automating as much of the architectural process as we can,” Marks stressed, “so the architects can do what they do best rather than worrying about the HVAC.” The company is at work on licensable proprietary software that Curtis says will be a “game-changer” for construction-pricing transparency by directly integrating design tools with Katerra’s supply and delivery line. The company is developing an energy system to modulate between the grid and photovoltaics to reduce energy costs.
“We as a team are thinking about designing space, but in the background we’re also asking, ‘Is this a wall panel I can repeat and use? How will it be made and how will it be trucked across the country? How does it connect to the floor plane?’ It’s as much about tectonics as architecture has ever been.”
The new tools and Katerra’s disruptive idealism drew Green into the partnership. An early proponent of mass timber, he is best known for two of North America’s largest CLT structures: the Wood Innovation and Design Centre in Prince George, BC, and T3, a 220,000-square-foot, seven-story office building in Minneapolis. He was the first member of a “design consortium” Curtis created to, as he put it, “keep us honest.” (Ted Flato of Lake|Flato and Andrea Leers of Leers Weinzapfel Associates have since joined as advisors.) The relationship with Green evolved into the design of Catalyst, a net zero–aspiring office/lab building, planned to open in Spokane in 2020, that will be the first to use CLT from Katerra’s new factory.
“It couldn’t be a better scenario,” says Green of the merger. “We get all of Katerra’s cool innovation capacity and R&D.” Architects, he added, “have done a great disservice by concentrating on those who can afford architecture rather than on making architecture affordable to more people. That is what is driving us toward the Katerra model.”
Ted Flato is equally “bullish on Katerra” but has also experienced the current limits of the company’s idealism. Long an experimenter in modular housing, Flato was adapting his prototype “Porch House” concept to Katerra’s production system last year—just as Hurricane Harvey walloped Texas, followed quickly by the Northern California fires. “I thought the catastrophes were real opportunities to provide more resilient housing fast,” Flato said. But with only one factory and dozens of apartment buildings already booked, Katerra has slowed its single-family efforts.
“They are business people, so they are focusing on apartments,” Flato said. “But their every effort seems to be to signal that design matters.”
Michael Green Architecture and Lord Aeck Sargent will retain their names and locations, but now as subsidiaries of Katerra. None of the parties disclosed the acquisitions’ terms.
Originally published on May 30, this story was updated on June 14.